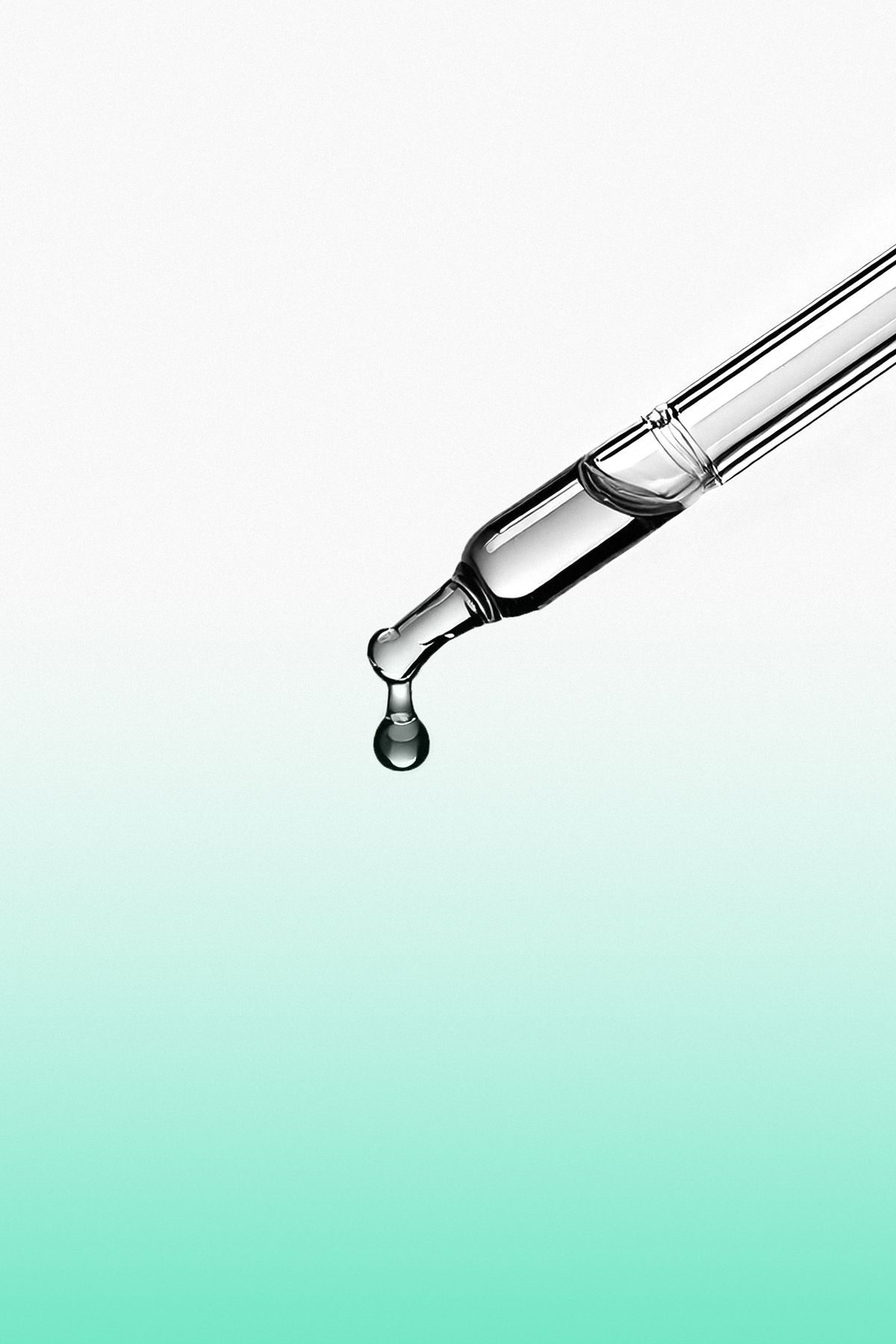
Andrew Lowenstein, OXON Technologies CEO, Meets with Power Progress International
- Article
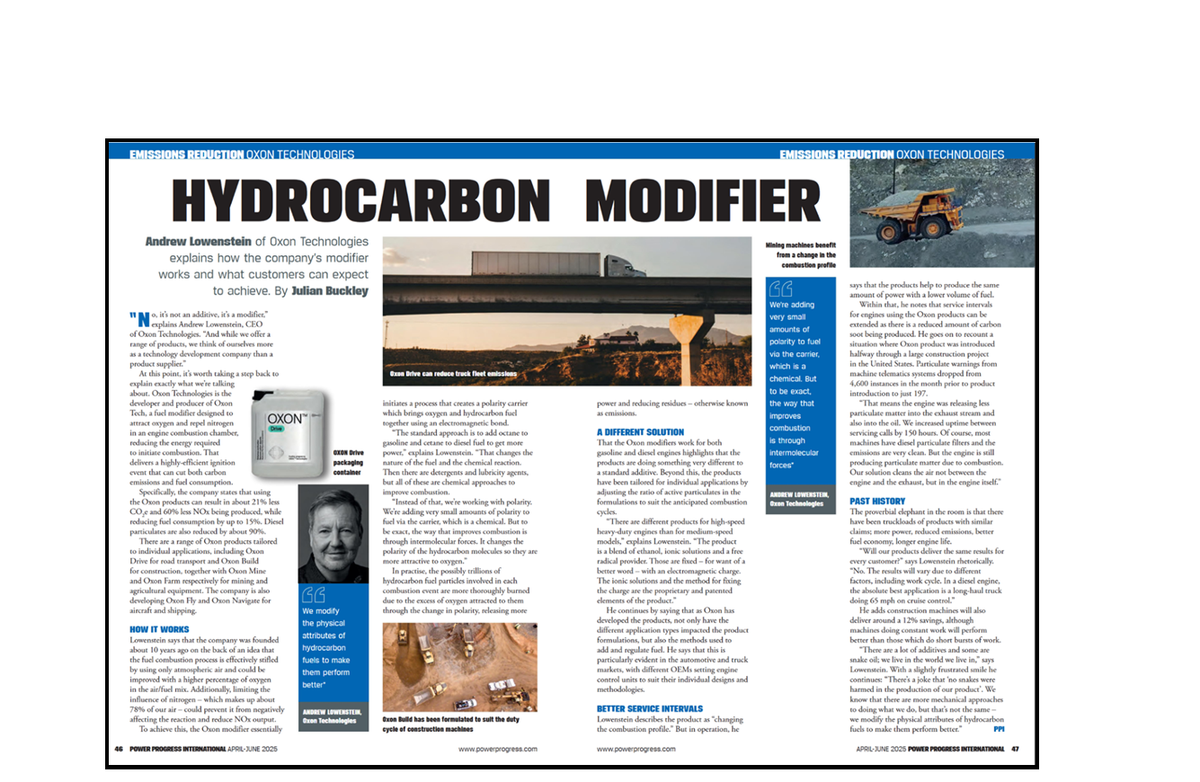
“No, it’s not an additive, it’s a modifier,” explains Andrew Lowenstein, CEO of OXON Technologies. “And while we offer a range of products, we think of ourselves more as a technology development company than a product supplier.”
At this point, it's worth taking a step back to explain exactly what we're talking about. OXON Technologies is the developer and producer of OXONtech, a fuel modifier designed to attract oxygen and repel nitrogen in an engine combustion chamber, reducing the energy required to initiate combustion. OXONtech delivers a highly efficient ignition event that can cut both carbon emissions and fuel consumption.
Specifically, the company states that using the OXON products can result in about 21% less CO₂e and 60% less NOx being produced, while reducing fuel consumption by up to 15%. The particulates are also reduced by about 90%. There are a range of OXON products tailored to individual applications, including OXON Drive for road transport and OXON Build for construction, together with OXON Mine and OXON Farm, respectively, for mining and agricultural equipment. The company is also developing OXON Fly and OXON Navigate for aircraft and shipping.
How It Works
Lowenstein explains that the company was founded about 10 years ago on the premise that the fuel combustion process is stifled by relying solely on atmospheric air. The idea was that combustion could be improved by increasing the proportion of oxygen in the air–fuel mixture. Additionally, limiting the influence of nitrogen—which makes up about 70% of atmospheric air—could prevent it from negatively affecting combustion and reduce NOx emissions.
To achieve this, the OXON modifier initiates a process that creates a polarity carrier, which binds OXON and hydrocarbon fuel together using an electromagnetic bond. “The standard approach is to add octane to gasoline and cetane to diesel fuel to get more power,” explains Lowenstein. “That changes the nature of the fuel and the chemical reaction. Then there are detergents and lubricity agents—but all of these are chemical approaches to improve combustion.”
“Instead of that, we're working with polarity. We're adding very small amounts of polarity to the fuel via the carrier, which is a chemical. But to be exact, the way it improves combustion is through intermolecular forces. It changes the polarity of the hydrocarbon molecules so they are more attractive to oxygen.”
In practise, the possibly trillions of hydrocarbon fuel particles involved in each combustion event are more thoroughly burned due to the increased oxygen drawn to them via this polarity shift. This results in greater power output and fewer residues, otherwise known as emissions.
A Different Solution
That OXON modifiers work for both gasoline and diesel engines highlights how the products differ from standard additives. Beyond that, the products are tailored for individual applications by adjusting the ratio of active particles in each formulation to match the anticipated combustion cycles.
“There are different products for high-speed heavy-duty engines than for medium-speed models,” says Lowenstein. “The product is a blend of ethanol, ionic solutions, and a free radical provider. The solutions are ‘fixed’—for want of a better word—with an electromagnetic charge.” The ionic solutions and the method for fixing the charge are the proprietary and patented elements of the product.”
He continues by saying that as Oxon has developed the products, not only have the different application types impacted the product formulations, but also the methods used to add and regulate fuel. He says that this is particularly evident in the automotive and truck markets, with different OEMs setting engine control units to suit their individual designs and methodologies.
Better Service Intervals
Loewenstein describes the product as “changing the combustion profile.” But in operation, he says that the products help to produce the same amount of power with a lower volume of fuel.
Within that, he notes that the service intervals for engines using the OXON products can be extended, and there is a reduced amount of carbon soot being produced. He goes on to recount a situation where OXON product was introduced halfway through a large construction project in the United States. Particulate warnings from machine telematics systems dropped from 4,600 instances in the month prior to product introduction to just 197.
“That means that the engine was releasing less particulate matter into the exhaust system stream and also into the oil. We increased uptime between service and calls by 150 hours. Of course, most machines have diesel particulate filters, and the emissions were very clean, but the engine is still producing particulate matter due to combustion. Our solution cleans the air not between the engine and the exhaust, but in the engine itself.”
Past History
The proverbial elephant in the room is that there have been truckloads of products with similar claims. "Will our products deliver the same results for every customer?" asks Loewenstein rhetorically.
"No. The results will vary due to different factors, including work cycle. In a diesel engine, the absolute best application is a long-haul truck doing 65 mpg on cruise control."
He adds that construction machines will also deliver around a 12% savings, although machines doing constant work will perform better than those which do short bursts of work. "There are a lot of additives, and some are snake oil; we live in the world we live in," says Loewenstein.
With a slightly frustrated smile, he continues: "There's a joke that 'no snakes were harmed in the production of our product.' We know that there are more mechanical approaches to doing what we do, but that's not the same—we modify the physical attributes of hydrogen fuels to make them perform better."
Written by Julian Buckley, Power Progress International, Q2, 2025
More news
- Press release
- Article
OXON™ Technologies announces $400 million Clean Fuels Investment Program with the United Arab Emirates
- Article
Fueling progress: cost-effective emissions reduction in ski resorts
- Article
OXON™ Technologies Announces OXON™ Grow and the Appointment of Paul-Evence Coppée as Vice President of Agriculture, Forest and Aquaculture Markets